
The Gecko is a fully integrated controller solution, so it saves you the headache of individual drive, and breakout board issues. The easiest way to get rid of what sounds more, and more like electrical problems is to rebuild the controller portion of the system tackling each section carefully.
#G540 CONTROLLER PROFESSIONAL#
Random problems should have been eliminated way before you ever used the machine in a professional capacity (this is my opinion, but one to really think about) The next thing we should talk about is the list of random problems you encounter with the system.

A dual core system is cheap enough now that anyone can afford one if sourced correctly online. I wouldn't recommend using less than a dual core system with at least 2gb of memory to have Mach3 perform as reliable as it should. The system is at best the bare minimum to run Mach3. The next area to review is the computer your using to run your system. Isolate the problem to the best of your ability, and eliminate each variable one by one till you notice a change be it positive or negative. If you built the system, part of building it is troubleshooting every area of it. Remember a red fault light on the Gecko is a sign something isn't correct. Changing motor cables can have a huge difference if after you perform your inspection, and can't identify an issue. Once that's done if your problem still continues I would start looking at the wiring of the motors all the way to the Gecko's DB9s. Make sure they are all connected securely. First, and foremost lets look at the Gecko producing a red light fault, that goes away after you unplug a motor or cycle a switch (Please specify which switch E-stop or on/off) If your encountering this I would look at your wiring with the motors first. Lets take a moment, and break your post up in sections to identify possible issues with your setup. No way to run a business if I cannot count on my machine making a cut correctly without fault.I'm a little lost on your post. Please help me - I am about to sell my whole computer, and electronics package and go buy all new. No way to run a business if I cannot count on my machine making a cut correctly without fault. In fact, I have started pulling a motor output every time I power up. I either have to cycle switch numerous times or unplug one motor from back of controller and fire it up without fault. This computer is not connected to internet, all updates are disabled and only Mach 3, Sheetcam and Autocad are essential programs installed.Įvery time i power up the controller box the G540 faults red LED.
#G540 CONTROLLER WINDOWS#
All ground wires are #8 solid.ĭell computer with Windows XP (service pack 3), Pentium 4, 3.2Ghz with 1 gig of ram. I have Gantry, control box, plasma cuttter, computer case and machine base all grounded to an 8' long - 5/8" ground rod drove in the ground right beside machine. I have ferrite chokes on all cables, limit switches.
#G540 CONTROLLER INSTALL#
to install the torch height control, I bought the G540 interface card to go with it and it is plugged directly into the G540 per the CandCNC Instructions. Power supply has internal cooling fan, but I also installed a separate fan on the box. Hypertherm 1250 plasma cutter with machine torch. I have candcnc LCTHC torch height control. Here are my specifics: I bought my G540, 3.81oz Nema 23 Stepper Motors and 48vDC Power Supply from Kelnig.
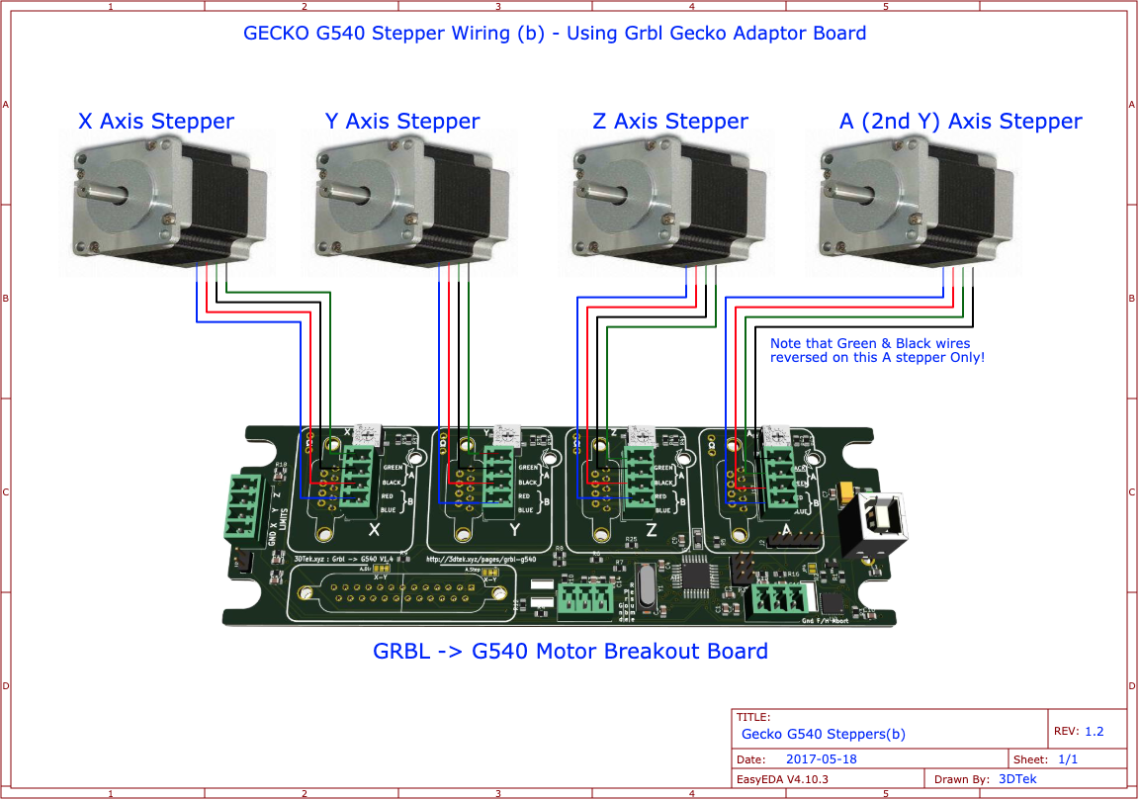
Stops next time torch is due to fire because of no Torch OK signal to controller.
